Az autó súlyának csökkentése
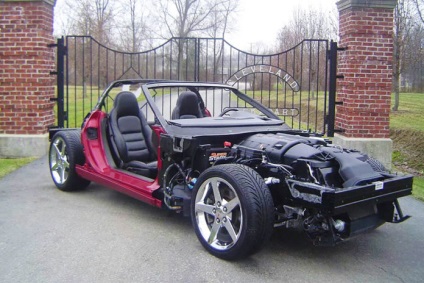
A káros anyagok kibocsátásának jogi korlátozása az autógyártók számára egyre több eszközt keres az üzemanyag-fogyasztás csökkentésére. Az egyik irányzat az autó tömegének csökkentése. A nagy autónak előnyei vannak - mindenekelőtt a biztonság és a kényelem. De a fejlődés vektorja megváltozott a gazdaság és az ökológia irányában. Ezért a fogyasztó figyelmét felhívja a figyelmet a könnyű autó előnyeire: könnyebb megoszlani és megállítani, könnyebb ellenőrizni, baleset esetén kevesebb kárt okoz más autóknak. Az autó súlyának csökkentése minden tíz százaléknál hat százalékos üzemanyag-megtakarítást eredményez.
Az ellenfelek azzal érvelnek, hogy az alumínium és a CFRP használata növeli a gép és a gyártók költségét, ezért jobban aggódnak a nyereségük miatt. És ugyanaz az alumínium termelése messze nem környezetbarát, és megakadályozza az autók kibocsátásának csökkentését.
De a tény továbbra is fennáll: minden nagy autógyártó tanfolyamot tartott a tömeg csökkentésére. És mindenekelőtt a testre vonatkozik. Könnyűszerkezete azt jelenti, hogy kompaktabb fékrendszer és motor, kisebb üzemanyagtartály és így tovább lehet használni.
A testek könnyítése több irányba megy: a testszerkezet optimalizálása, a könnyű anyagok használata és az új gyártási folyamatok bevezetése. Ez utóbbiak közé tartozik például a lézeres hegesztés, súrlódás, vagy az alkatrészek előállításának módja forró bélyegzéssel vagy hidroformálással.
Könnyű anyagok a modern autó testek
A modern testek gyártására szolgáló fő anyagok a nehéz acélok és az alumínium. És az acél szilárdsága az elmúlt két évtizedben időnként növekedett, és az alumínium ötvözetek - negyedével. Az alumínium szélesebb körű felhasználását magas áron tartják vissza. De az olyan óriások, mint az Audi, a BMW és a Mercedes egyre nagyobb figyelmet fordítanak az összetett anyagok kifejlesztésére és kivitelezésére.
A kompozit anyag olyan anyag, amely megerősítő és kötő komponenseket tartalmaz. A megerősítés a részek szilárdságát és merevségét, valamint a kötőanyagot - a kívánt alakot adja. Fontos feltétel az erősítő szálak elhelyezése szigorúan az alkalmazott terhelés irányában. Ha az erő a szálakon át irányul, az összetétel nem marad túl. Ezért, ha ismeretes az alkalmazott terhelések iránya, akkor a rostok helyzetének megváltoztatásával könnyű létrehozni a kívánt jellemzőkkel rendelkező részt.
A kompozitok jobb szilárdságú és szilárdsági tulajdonságokkal rendelkeznek, mint a nagy szilárdságú acél. A lengéscsillapításnál a megerősített műanyagból készült cső nem roskad össze, mint az acél, de teljesen összeomlik. A szénszálak által elnyelt fajlagos energia négyszer akkora. Miért van még mindig széles körben elterjedt a testek létrehozásában az ilyen szempontból ideális eszmény? Több oka van: magas ár, alacsony gyárthatóság, nincs jelentős nyereség a súlyban. Például a szén-műanyagban nem kívánatos a lyukak fúrása, mivel az erőtől sokkal nagyobb mértékben esik az acél.
De a technológiai áttörés valószínűleg összetett anyagokban fog bekövetkezni. A BMW, például úgy vélik, hogy a támasztóköpeny elég lehet tenni két vékony lapból kompozit, a tér között van töltve alumínium méhsejt vagy habosított polimer. Az ilyen kísérleti technológia által gyártott M3 motorháztető súlya mindössze 5 kg! Egyelőre kisebb terhelésű elemeket készítenek a kompozitokból, például különböző típusú záróelemekből. Ugyanolyan szilárdságúak, sokkal könnyebbek az acélhoz és az alumíniumhoz. A szén műanyag fékek kétszer olyan könnyűek, mint az acél fékek, de sokkal drágábbak, és ami a legfontosabb, csak fűtést követően hatnak.
A testsúlymérő mérnökök mérnökei nem csak a testben találják meg. Például a Ford mérnökei csökkentették a műanyag súlyát is! Az ötlet lényege, hogy a gázbuborékok befecskendezése a műanyag részek előállítása során történik: a porózus csokoládéhoz hasonló szerkezetet hoznak létre. A kis "üres" tereknek köszönhetően a rész könnyebbé válik az integritás elvesztése nélkül.
És most - csak azokat a tényeket, amelyek világosan illusztrálják a szakértők leleményességét a fogyás kérdésében (anélkül, hogy konkrét modelleket és gyártókat adnának meg).
A magnézium, amely a kormánykerék kialakításánál használt, 400 grammot mentett meg. A sebességváltóban az egyedi alumínium részek magnéziummal való felváltása 760 grammot vett el. vezetékek elrendezése optimalizálás segített csökkenteni a hosszát, és mentse 2,68 kg, műanyag kosár és neodímium mágnessel hangszórók hangszóró rendszer mentette a kilogramm. Az alumíniumagy és az öntöttvas kombinációja lehetővé tette a súlycsökkentést 20% -kal az acélfékekhez képest. A habpolimerből készült betétek a kerék súlyának 1,5 kg-os csökkenését eredményezték.