Vizsgálati munka - öntés
1. Válassza ki a munkadarabokat.
1.1 meghatározzuk az öntés méretpontossági osztályait a 9. táblázatból [1; pp. 32-35]. Elfogadja a 9. fokozat pontosságát
1.2 Válasszuk ki az öntőelemek warpage-fokát a 10. táblázatból [1; 35. oldal] Elfogadjuk az öntvény 5, az L = 100 minimális átmérő
1.3 Adja meg az öntvény felületének pontosságát a táblázatból. 11 [1; pp. 36-38]. Elfogadjuk az öntvény felületének pontosságát 14
1.4 meghatározza az öntvény tömegének pontossági osztályát [1; 40. oldal]. Mivel a rész tömege m = 5,5 kg, az öntvény tömegének pontossági osztálya 8-nak felel meg
1.5 Határozza meg az öntvény elmozdulásának tűrését a csatlakozó síkja mentén a táblázatból. No. 1 [1; oldal 2-3]. Az előfeszítési tűrés = 0,64 a 4. oldalon lévő 2.7. Pont szerint történik
1.6 Meghatározzuk az öntvény lineáris méreteinek toleranciáját a kezelt felületekre:
A ø16 lyukak nincsenek leadva
1.7 Határozza meg a feldolgozáshoz szükséges összes kibocsátási egységet, ezért meghatározzuk az öntvények kibocsátási egységeinek számát [1; 43. o.] A 6. átlagértéket vesszük a 6. táblázatból [1; 10], meghatározzuk a dimenziók teljes kibocsátási egységeit, a felületi elem teljes tűréseitől függően.
A 18-as méretű, 1,6-os teljes tűréshatár mellett az oldalkülönbség 2,2 lesz
A ø36-2,3 mérethez

A bárok dobozokkal vagy sablonokkal kaphatók. A kész rudakat speciális kemencékben (szárítókban) szárítják, hogy növeljék erősségüket, gázáteresztő képességüket, valamint csökkentsék a gáztermelést. Az öntvénybe való beszerelés előtt a rudakat tűzálló anyagokból álló festékekkel festették: grafit, porított kvarc, cirkon deiron stb., Ami szükséges az öntvény felületének tisztaságához.
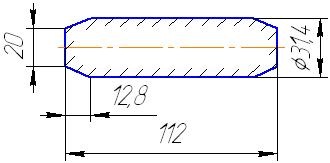
A rudakat elsősorban lyukak és üregek készítéséhez használják öntvényekben, valamint komplex konfigurációjú öntvények külső felületét.
Az öntés során a rudakat általában minden oldalról folyékony fém veszi körül. Ezért nagy gázáteresztő képességgel, szilárdsággal, megfeleléssel és kiütéssel kell rendelkezniük, amelyet a megfelelő magkeverék és a rúd kialakítása biztosít.
A rudak öt osztályba vannak osztva a geometriai méretek, a kialakítás, az öntőforma munkakörülményei és az öntött felület minőségi követelményei szerint.
I osztályú rudak, amelyek összetett kialakításúak, nyitott munkákkal rendelkeznek, és kisebb értékeket alkotnak az öntvények kezeletlen üregeiben, amelyek tisztasága magas követelményeket támaszt, például az övtípusú rudak a belsőégésű motorburkolatok öntéséhez.
II. Osztályú - komplex konfigurációjú rudak, amelyek masszív részekkel együtt vékony vetülettel, hidakkal rendelkeznek. Teljesen vagy részben megmunkált felületeket képeznek az öntésben.
III osztály - közepes komplexitású rudak masszív jelekkel, amelyek nem rendelkeznek különösen finom részekkel, de az öntvények üreges öntvényeit hajtják végre, a felület tisztaságának növelése érdekében.
IV osztály - egyszerű konfigurációjú rudak, amelyeket a feldolgozott és kezeletlen felületek alakjában állítanak elő, amelyek tisztaságára nem mutatnak különleges követelményeket.
V osztály - masszív rudak, amelyek nagy üregeket képeznek nagy öntvényekben.
Az I. osztályú rúdak keverékének nagy szilárdsággal, felületi keménységgel, magas nedvességtartalmú, minimális gáztartalommal, jó megfeleléssel és kiütéssel kell rendelkeznie.
A II. Osztályú rudak keverékének meg kell felelnie ugyanazon követelményeknek, de tartósabbnak kell lennie nedves állapotban, hogy a rúd masszív és magas része ne csökkenjen saját súlya alatt.
A III. Osztályú rudak keverékének nagy szilárdságúnak kell lennie nedves állapotban, jó megfelelésben és kieséskor.
A IV és V osztályú rudak keverékének nagy nedvességtartalmú, jó megfelelésű és kieséses szilárdságúnak kell lennie.
A rudakat kézzel vagy gépekkel gyártják dobozokban, ugyanazokkal a technikákkal, mint a formázáshoz. Az öntöde ágát, amelyben a rudak készültek, a magnak nevezik.
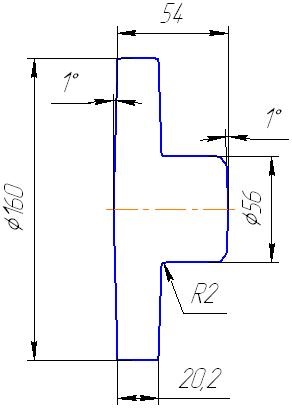
A modellt az öntöde modellboltjában vagy modellezési részlegében gyártják
A modell olyan eszköz, amely nyomtatás formájában érhető el, amely megfelel az öntvény konfigurációjának és méreteinek. A modellek fából, fémből, gipszből, műanyagból és más anyagokból készülnek.
A hüvely modell két félből áll, amelyek egymással kölcsönösen összpontosulnak tüskékkel és fészkekkel.
A hüvely furatát a 2 rúd állítja elő. A rúd a szerszám része. Egy magkeverékből készült, dobozba zárva. A dobozból való eltávolítást követően a rudat kemencében szárítják. Az öntőforma összeszerelésekor a száraz rudat a megfelelő szerszámüregekben rúdjelekkel szerelik fel, amelyeket a modellszimbólumok segítségével kapnak. A rúd hossza nagyobb, mint az öntőüreg hossza a jelek nagyságával.
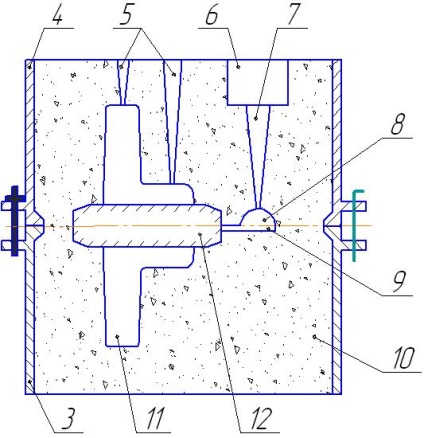
A persely formája két félformából áll össze: a felső és az alsó. A félkész formák öntvényből készülnek, öntöttvas vagy acél 4 és 5 acél keretben, amelyeket lombikoknak neveznek (felső és alsó).
A persely öntése. Az alsó lapon szereljük fel a modell felét, amelyhez az alsó félforma formában van egy lenyomata, valamint egy lombik. A 11 modell felületét és a pajzsot elválasztó folyadékkal megszórjuk vagy bepermetezzük, majd a 10 formázóelegyet a lombikba öntjük és tömörítjük. A fröccsöntési keverék feleslege felhordódik a tömörített félformából, a lombikot 180 ° -kal elforgatjuk és az alsó lemezre helyezzük. Ezután a modell felső felét a modell alsó felére helyezzük, a felső felét az alsó formára helyezzük. Ismét megszórjuk a modell felületét elválasztó homokkal, töltsük fel az öntözőrendszer modelleket, töltsük fel a formázó keveréket a felső lombikba és kompaktuk.
Távolítsuk el a felső félformát, távolítsuk el a modellek felét, szereljük be a rudat és gyűjtsük össze az alakot. A lombik alakjának összeszereléséhez speciális hüvelyek vannak, amelyekbe a központosító csapok belépnek. A forma öntése közben folyékony fémből présel a penészfalakon, aminek következtében a felső szerszám felemelkedhet, majd egy rés alakul ki a csatlakozó síkja mentén, amelyen keresztül a fém kifolyhat a szerszámból. Ennek megakadályozása érdekében a felsõ félforma az alsó konzolhoz van kötve, és néha a terhelést a felsõ formára helyezzük.
A folyékony fém öntése során az öntőüregbe a bevágócsatornákon keresztül jut be. Az öntőformába fémt előidéző csatornák rendszere szivárgásnak nevezhető. A futórendszer egy felszálló 7 (függőleges csatorna), egy 8 salakfelfogó és egy 9 adagolóból áll, amelyen a fém belép a szerszámüregbe. A kapunyitó rendszer tartalmaz egy 5 nyílást is. A fej szolgálja a levegő és a gáz formájának kilépését, valamint a fém öntvény fémmel való töltését.
A fém megszilárdulása és hűtése után az öntőforma megsemmisül, és az öntést kiszabadítjuk a formázó keverékből, a kapukat levágjuk és az öntvény felületét megtisztítjuk a formázó keverékből.
A megfelelően kialakított kapunyújtó rendszernek meg kell felelnie a következő követelményeknek:
gondoskodni kell arról, hogy a penész jó fémmel töltse és az öntést a szilárdulás folyamatába táplálja;
a pontos méretű öntvények gyártásának megkönnyítése, felületi hibák (eltömődések, összenyomódás, salak zárványok stb.) nélkül;
elősegítik az öntvény irányított szilárdulását;
A fémfogyasztásnak minimálisnak kell lennie.
A formák készítésének folyamata formázásnak számít. Ezt az öntödei öntőformákban végezzük. A rudakat a rudatartóban készítik el, és a formázóegységbe táplálják a formázó rekeszben. A öntvények előállításának legfontosabb szakasza a penészgombák, rudak és öntőformák gyártása. Az öntvények több mint 80% -át egyetlen öntési formában állítják elő, mivel a gyártásuk költsége meglehetősen alacsony, ugyanakkor felhasználhatók a leggyakoribb fekete és színes ötvözetek öntvényei előállítására, szinte bármilyen konfigurációra, összetettségre és tömegre.
A következő formázási módszereket alkalmazzák:
a talajban és a caissonban;
a csontváz modellek és a vezérlőszekciók;
gyors keményítő keverékek alkalmazásával.
Az öntőformák gyártási folyamatának mechanizmustól függően három formázási forma különböztethető meg: kézi, gépi és automata. Gépgyártó üzemekben a kézi öntést egy vagy több öntvény előállítására használják, például a kísérleti gyártás körülményei között, egyedi öntvények gyártásánál, valamint javításra is. A gépi öntvényeket az öntvények sorozatos és tömeggyártása, illetve az öntvények öntésére szolgáló eljárások (automatizált automata gépek) automatizálásához használják.
Az öntödei gyártásban a formázás széles körben elterjedt a lombikokban, főként osztott modelleken, és a formázást leggyakrabban kettőben hajtják végre, és ritkábban három vagy több lombikban. Az öntvények öntvények alakításakor pontosabbak, mint a talajban történő kialakításnál, mivel a lombikok csapok közé vannak helyezve.
A lombikok kialakítása sokkal hatékonyabb, mint a talajban történő öntés. Többféle öntési módszert alkalmaznak:
hamis fedéssel;
flip-flopral;
több lombikban;
levehető alkatrészekkel.
Formázás két lombikban egy osztott modellen. A formagyártás folyamata a modell telepítésével vagy annak felével kezdődik a modelllapon. Ezután egy üres palackot helyeznek a lemezre, és a modell felületét petróleum keverékkel nedvesítik, vagy finom homokkal porították. Ezután a béléskeveréket átszitálják egy kézi szitán. A béléskeverék rétegének vastagsága kis öntvények esetén 15-30 mm, a nagyobbak pedig 30-40 mm. Magas, puszta falakkal rendelkező nagy öntvények kialakításakor a béléskeveréket szitán átszitálják csak a modell vízszintes síkjának fedésére. A puszta falak burkolását ugyanazzal a bevonó keverékkel állítják elő. A töltőanyagot a lombikba töltjük és tömörítjük. Az öntőforma egységes sűrűségének elérése érdekében a töltőelegyet rétegekbe (57-75 mm) öntjük a lombikba, és kézi vagy pneumatikus dörzsöléssel tömörítjük. A tömítésnél lehetetlen megakadályozni a merevítőt a modellen, mivel a fröccsöntő keverék az ütközési helyeken erősen tömörödik, és gázkagyló alakulhat ki az öntvényekben. Különösen óvatosan, a keveréket tömöríteni kell a sarkokban és a lombik falai közelében.
A felesleges öntőkeveréket tömörítés után rake vonal szintben a széleit a lombikba, és Duszniki Pierce szellőzőcsatornákba úgyhogy dushnik nem érte el a modell 10-15 mm. Ezután a lombikot a modelllemezzel együtt 180 ° -kal elforgatjuk, és a modell második felét beállítjuk.
Annak érdekében, hogy megszüntesse a felső öntőforma öntőforma keverékének az aljához való tapadását, az alsó félforma síkját száraz elválasztó homokkal tölti. Ez a homok sűrített levegővel lefújja a modell felületét. A felső lombikot az aljára helyezzük, és a homlokegyenest tartalmazó réteget egy szitán keresztül öntjük a modellre, felhúzzuk a felszedő modelljét és töltsük a keveréket. Ezután kompenzálja a keveréket. A többlet összekeveredik a rake-ot és csinál rossz dolgokat.
A szerszámot felnyitják és nedvesítik vízzel a modell közelében. Ahhoz, hogy megakadályozza a folyékony fém elhagyó penész öntés közben a nyers, hogy kialakítsuk a osztásvonal do kockázatok (trimmelés) a modell körül a távolság 50-70 mm-re vannak. Ha fém-öntjük a száraz formában, és különösen, amikor a lombikokban levő nem kielégítő a legtöbb esetben a gépen alakú csatlakozót egy vékony réteg agyag, amely, amikor párosodás a szerszámfelek kiküszöböli fém Provo alakjukat. A modelleket nem szabad a Paradicsom paradicsoma közelében találni; a távolság a modell a lombik faláról kell Byl legalább 25-50 mm súlyától függően és méretei az öntési lombik méretben.
A modell csavarozott vagy kalapált. Ezután kissé lenyomják a kalapács fújását a felemelkedéstől, és formájukat kivonják. A kivezető rendszer elemei, emelő, fej, adagoló elemek is kivonásra kerülnek. A kis modelleket kézzel, a nagydarabokat pedig egy daru segítségével vették ki.
A modell kivonása az űrlapról felelős művelet, és nagyon óvatosan kell elvégezni, hogy ne tegyék el az űrlapot. A modell erősen benyomása nem ajánlott, mert ugyanakkor az öntvények nagyobb méretű és súlyúak.
A modell eltávolítása után a penész felülete el van vágva. A formák helyesbített helyeit simítóval, kanalakkal, lancettekkel stb. Korrigálják. Az alak egyes részeit megerõsítik a szegecsekkel. A kész formát, nyersen elkészítve, porított grafit vagy szénporral megszórjuk a szerelés előtt. Száraz módon öntött formában a penész felülete nem porított, hanem festett. A formákat általában szárítás után festik, amikor a formát még nem hűtik. Néha az űrlapokat kétszer festik: a szárítás előtt és után. Ezután a rúd össze van szerelve, és a szerszámot összegyűjtik.
Formázás két lombikban egy all-in-one modellel. Egy kis fedelet egy fából készült egy darabból állítanak elő. Először formáld az alsó lombikot. A fadobozra egy modellt és egy alacsonyabb lombikot helyeznek, majd a formázó keveréket öntik és tömörítik. Lombik lemez 180 ° -kal elfordítani, állítsa be a felső lombikot és a minta kapuzó rendszer, és szintén hozzáöntjük a felső öntvény lombikba és a keveréket tömörítjük. Ezután emeljük fel a felső félformát, fordítsuk 180 ° -ra, és kivesszük az alakjuk modelleit. Ezután az alakot eltakarják, összegyűjtik és fémmel töltik.
A gépi formázást főként a tömegtermelésben és a tömeggyártásban használják, és kevésbé gyakori a kisléptékű és egyszeri gyártásban. A gépi öntést általában két lombikban hajtják végre, kivételt képeznek a bolyhok alakítása és a formázatlan formázás.
A forma általában két félformából áll - a felső és az alsó. A gyártás a formák a gép kell modell, modell lemezeket, két acél palackok, csapokat. A tömeg és a térfogat termelés használt fém modell sorozatgyártása - fából készült modellek, megerősített a koordináta lemezeken. Minden esetben, a formázó végezzük a gépek modell szerelt a fémlemezek, ami növeli a pontosságát az öntvények, és a gépesítése fő műveletek (penész tömítő és extrakciós modell) teljesen felszabadítja alakítója munkaigényes kézi műveletek.
Fröccsöntő gép, mint a kézi számos előnye van: a magas termelékenység, precíziós öntvények, és ennek következtében kisebb ráhagyás, egységességét a tömítés formája, a képesség, hogy munkát végezzenek alakítója alacsonyabb képesítést.
A pontosság öntvények méreteket képező gép használatával érik el pontosabb (kisebb eltérésekkel) modellek helyett lépést a taszítás rezgés modellek, ha kivesszük a formából, egy jó központosító palackokban.
Háromféle típustáblát használnak a gép formázásához:
egyoldalas - az egyik lemezen a modell alsó része, a másik pedig a modell felső része; 2) kétoldalas - a tetejére szerelt modell egyik oldalán, a másikon - alul (egy gépen kialakítva);
reverzibilis - az alsó és a felső formák egy lemezre öntöttek, és a felső lombik összeállításakor 180 ° -kal elforgatják.
A modellek állandó rögzítése a lemezekre tömeges és nagy léptékű gyártásban történik. Kisméretű gyártásban alkalmazzák előregyártott modelllapokat, amelyek modellekkel rendelkező betétekből állnak; koordinálja a modelllemezeket - egyetlen és kis méretű gyártásban. A koordinátalemezek lyukakkal rendelkeznek a modell telepítéséhez és a pozíció helyességének meghatározásához. A lemezen levő lyukat a betűkkel és számokkal alkotott titkosítás jelöli. Ezzel a titkosítással telepítse a modelleket a tűzhelyre.
A gépek formázására szolgáló technológiai folyamat számos műveletből áll.
Alapvető Működés - tömítő a formázható keveréket a lombikba, és extrakciós mintát a penész minőségét meghatározzák jövőbeli öntésnél: jelenléte az ott elzáródások, lyukakat, repedéseket; A geometria helyességi; felület tisztasága.
Háttér és szállítási műveletek - beállítunk egy üres lombikot a gépen, a permetezés és a robbantási minta lemez, kitöltve a formázható keverékhez a lombikban, szállítására kész formák - végzik speciális kisegítő gépek és közlekedési mechanizmusok.
Mértékétől függően a gépesítés és a kiegészítő szállítási tevékenységek különböztethető meg: 1) a gépesített öntés, ha dolgozik kézzel vezérli a működését mechanizmusokat, amelyek elvégzésére a fő, kiegészítő és szállítási műveleteket, valamint 2) az automatikus formázás, ha a működési mechanizmusát működik a gép.
A legnehezebb és leginkább felelős a penész lezárásának és a modell kivonatolásának a művelete.
Számos módszer létezik a tömítő a formázható keverékekből gépek: tömörítés, kompressziós rezgés, remegés, vortexeléssel a elősajtoló, peskometom, pressin-peskoduvny.
Adja meg a felületkezelési sémát 1,2,3 részből, amelyek rajza a 2. ábrán látható. Minden séma esetében adja meg a gép, eszköz és jig nevét. Húzza ki a szerszám vázlatát a 3 felület és a munkadarab rögzítéséhez szükséges eszközzel az 1 felület megmunkálásakor.
Anyag öntöttvas Ч20 GOST 1412-85
1. táblázat - Kémiai összetétel