A kőolajkoksz és az iparban használt nyersanyagok előállításának technológiája
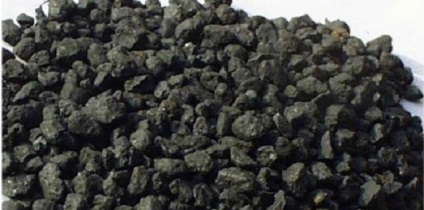
Ásványolaj koksz gyártására szolgáló nyersanyagok
A nyersanyagok minősége elsődleges hatással van a végtermék - kőolajkoksz jellemzőire.
A CIS-ben a koksztermelést elsősorban a késleltetett kokszolóüzemek (UCS) végzik.
Az UZK működési feltételeinek egyik jellemző tulajdonsága, hogy az olajfinomítás eredményeképpen a növényekben maradt különböző keverékek nyersanyagként használják.
A nyersanyagok nehézolaj-frakciók eredő légköri és vákuumdesztillációval, olaj (fűtőolaj, polugudrony, kátrány), krakkolási maradékokat a termikus krakkolás tüzelőolaj és kátrányok, nehéz gázolajok, katalitikus krakkolás, maradék olaj gyártás (aszfalt propán aszfaltmentesített tar, kinyeri a fenol tisztítására olajok és et al.).
Különböző típusú koksz struktúrák kialakulásához hajlamosító összes olajos maradék közül az aromás koncentrátumok (desztillátum-krakkolási maradék) és más nagy molekulatömegű szénhidrogének a legelőnyösebbek.
Emiatt a desztillátum nyersanyagai ígéretes nyersanyag-típusokra utalnak.
A finomítók különböző termelési feltételekkel rendelkeznek, és különböző olajokon működnek, így minden egyes finomító esetében a későbbi kokszolóüzemek speciális körülmények figyelembevételével épültek.
Az olajok minőségét meghatározó fő paraméterek közül, mint a kőolajtermékek sűrűsége, frakcionált és kémiai összetétele, a legfontosabb a kéntartalom sűrűsége és indexe.
Kén - az egyik legkívánatosabb szennyeződés a nyersolajok összetételében és a végtermékben - koksz.
A kén tömegtöredékétől, a koksztól és az olajtól függően alacsony kéntartalmú, kénes, magas kéntartalmú anyagokat sorolnak be.
Kén kokszok különböznek kevésbé kedvező tulajdonságokkal mint alacsony kéntartalmú koksz: oka berendezések korrózió, megnövekedett számú repedések a elektród termék, a pusztítás a tűzálló falazat kemencékben, így használatuk korlátozott, hogy bizonyos területeken.
Az olajtartalmú finomítókba belépő olaj összetételenként változik, különösen a kéntartalom tekintetében.
Oroszország esetében elsősorban a kénes és a savanyú olaj feldolgozása jellemző.
Jelenleg a koksz termelésének fő nyersanyaga a kén-dioxid.
Az olyan technológiák alkalmazása, amelyek lehetővé teszik minőségi koksz beszerzését, függetlenül a kiindulási olaj összetételétől, számos problémát megold:
kiváló minőségű nyersanyagokat biztosít az elektródaipar számára, lehetővé teszi számunkra, hogy szélesebb körű olajokat használjunk a termelésben, és mélyítsük el az olaj finomítói finomításának folyamatát.
A végtermék kénmentesítésére a koksz kalcinálását alkalmazzák.
A kéntelenített kőolaj kokszból előállított kénvegyületek másik módja a kéntartalmú kőolaj kéntelenítése, hidrokrakkolása vagy deaszfaltálása.
Ezt az opciót hatékonyabbnak tekintik, annak ellenére, hogy összetettebb és további költségeket igényel.
Az orosz növények olajat szállított főleg fő vezetékek (MNP) Transneft, ahol a nyugat-szibériai olaj, Szibériai Fény márka összekeverjük az olajjal és nehezebb kénes Urál jelet.
Nyers és kalcinált kőolaj koksz előállítására szolgáló eljárások
A kőolaj kokszolása az olajmaradványok termikus repedésének legsúlyosabb formája.
Alacsony nyomáson és 480-560 ° C hőmérsékleten végzik el, hogy petrolkokszot, valamint szénhidrogén-gázokat, benzineket és kerozin-gázolaj-frakciókat kapjanak.
A kokszolás során a nyersanyag minden összetevője feloszlik, hogy folyékony desztillátum frakciókat és szénhidrogén-gázokat képezzen; a kerozin-gázolaj-frakciók intenzív kibocsátásával rendelkező szénhidrogének megsemmisítése és ciklizálása; a szénhidrogének kondenzációját és polikondenzációját, valamint a nagy molekulájú vegyületek mély tömörödését folytonos koksz-maradék képződésével.
Ipari kokszolási eljárás hajtjuk végre a növényekre 3 típusok: időszakos kokszoló koksz kockák, késleltetett kokszoló kamrák, folyamatos fluidizált ágyas kokszoló hordozót koksz.
A késői (semikontinuált) kokszolás a világ gyakorlatában a legelterjedtebb.
Nyersanyag, előmelegítjük csőkemencébe, hogy 350-380 ° C-on, folyamatosan adagoljuk a lépcsős tálca desztillációs oszlop (működtetett atmoszférikus nyomáson), folyik le, amely érintkezik a gőzök felé emelkedő szolgáltatott a reakció berendezésben.
Ennek eredményeként a hő- és anyagátadó része a gőz kondenzálódik, alkotó a nyersanyaggal úgynevezett másodlagos nyersanyagként, amely melegítjük csőkemencében, hogy 490-510 ° C-on, és belép a kokszoló kamrák - egy üreges henger alakú függőleges készülék átmérője 3-7 m és a magassága 22-30 m.
A kamrában a reakcióedényt folyamatosan táplálják 24-36 órán át, és az általa halmozódott hőnek köszönhetően elkeverik.
Miután a kamrát 70-90% -ban koksszel töltötte, általában nagynyomású vízsugárral (max. 15 MPa) távolítja el.
A koksz belép a darálóba, ahol legfeljebb 150 mm-es darabokra őrlik, majd a felvonót a képernyőre táplálja, ahol a 150-25, 25-6 és 6-0,5 mm-es frakciókra oszlik.
Az a kamrát, amelyből a kokszot kirakodják, forró vízgőzzel és gőzzel melegítik a működő kokszkamrából, és újra töltött tömeggel töltik fel.
Az illékony anyagokat kokszoló képviselő gőz-folyadék keveréket folyamatosan kivezetjük a kamrák és jár egymás elválasztva egy desztillációs oszlopban, vízelválasztón, és a gázszelep a sztripper gázok
A folyamat tipikus paraméterei: a kamrák hőmérséklete 450-480 ° C, a nyomás 0,2-0,6 MPa, az időtartam 48 óra.
A késleltetett kokszolás előnyei - az alacsony hamutartalmú koksz magas hozama.
Ugyanilyen mennyiségű nyersanyagból ez a módszer 1,5-1,6-szor több kokszot termel, mint a folyamatos kokszoláshoz.
Az orosz finomítók 1-blokk és 2 blokk kokszoló üzemet (minden egység 2 vagy 3 reaktort tartalmaz) többféle típusú.
A növények elrendezése és kialakítása a Giproneftezavod és VNIPIneft intézetek projektjeinek megfelelően történt.
Vízszintes hengeres berendezésben, 2-4 m átmérővel és 10-13 m hosszúsággal vezetik.
A kocka alapanyagait fokozatosan fűtik az alatta nyílt tűzzel.
Ezután a desztillátumokat szokásos módon elkülönítjük, a kokszot szárítjuk és kalcináljuk (2-3 óra).
Ezután a kád alatt lévő kemence hőmérsékletét fokozatosan csökkentjük, és a kockát először vízgőzzel, majd levegővel lehűtjük.
Amikor a koksz hőmérséklete 150-200 ° C-ra esik, akkor lemerül.
Jellemző folyamatparaméterek: hőmérséklet a gőzfázisban 360-400 ° C, légköri nyomás.
Ez az eljárás azonban azt mutatja, az alacsony hatékonyság, megköveteli a sok üzemanyag-fogyasztás, valamint a jelentős költségeket a kézi munka, és ezért alig használják az iparban.
Folyamatos kokszolás a fluid ágyban (hő kontaktusos krakkolás)
Nyersanyag, előmelegített a hőcserélő érintkezésbe egy reaktorban, és melegítjük szuszpenzióban inert hűtőközeg és koksz a felszínén alatt 6-12 perc.
Hőhordozóként általában 0,3 mm-es szemcseméretű porított kokszot használnak, ritkábban nagyobb granulátumokat.
Az így kapott kokszot és hűtőfolyadékot eltávolítjuk a reakciózónából, és regenerátorba (kokszolókemence) tápláljuk.
Ott a hűtőfolyadékot levegő segítségével szuszpenzióban tartják, amelynek áramában a koksz legfeljebb 40% -a elégetik, és a legtöbbjük a fogyasztó felé irányul.
A koksz egy részének égése során felszabaduló hő miatt a hőhordozót felmelegítik és visszatesszük a reaktorba.
A hűtőfolyadék mozgatásához a gőz vagy gáz gázáramával befogott kokszrészecskék pneumatikus szállítását alkalmazzák.
A desztillátum frakciókat és gázokat kivonjuk a reaktorból, és a késleltetett kokszolással azonos módon elválasztjuk.
Tipikus eljárás paraméterei: hőmérséklet hőcserélő reaktorban 300-320 ° C 510-540 ° C és 600-620 ° C A regenerátor nyomás a reaktorban és a regenerátor 0,14-0,16 és 0,12-0,16 MPa hűtőfolyadék - (6,5-8,0)
A fluidágyban a kokszolás a könnyűolajtermékek hozamának növelésére szolgál. Ezenkívül a folyamatos kokszolás kombinációja a kapott koksz gázosításával dízel és kazán tüzelőanyagok előállítására használható.
Használat előtt a petrolkoksz általában finomítható, beleértve számos folyamatot.
Kalcináláskor az illékony komponenseket és részlegesen heteroatomokat (például kén és vanádium) eltávolítják, a fajlagos elektromos ellenállás csökken.
A grafitizálás során a 2D kristályokat kristályos formáikká alakítják 3-dimenziós rendezéssel.
Általában, a finomítási szakasz lehet, amely az alábbi séma szerint: A krisztallitok → karbonizálás (kalcinálás 500-1000 ° C) → kétdimenziós rendelési szerkezet (1000-1400 ° C) → predkristallizatsiya (transzformációs krisztallitokat 1400 C felett) → kristályosítással, vagy grafitizált (2200-2800 ° C).
- alumíniumipar, mint redukálószer (anód tömeg) az alumíniumércek (bauxitok) alumíniumának olvasztásakor. A koksz fajlagos fogyasztása 550-600 kg / t alumínium.
- nyersanyagok acélipari kemencékben használt elektródák gyártásához;
- nyersanyagok karbidok (kalcium, szilícium) előállítására, amelyeket acetilén előállítására használnak;
- csiszolóanyagok, csiszolóanyagok előállítása,
- vezetékek, tűzálló anyagok gyártása stb.
- redukálószerekként és szulfidálószerekként (szulfidok és savak),
- agresszív közegek, rakétatechnológia stb. körülmények között működő vegyi anyagok gyártásához, stb. (szerkezeti anyag).