Víz blokk "győzelem"
Minden nap egyre gyakoribbá válnak a vízhűtési rendszerek. A gyártók egyre több készenléti megoldást bocsátanak ki. Azonban nem titok, hogy minden rendszer többé-kevésbé elfogadható áron veszít jó léghűtőket, amelyek gyakran sokkal olcsóbbak és sokkal könnyebbek a telepítéshez és működtetéshez. Azok a rendszerek, amelyek igazán jobbak a levegőhűtéshez képest, legalább kétszáz euróért költenek ügyfeleket. Nem minden felhasználó engedheti meg magának ilyen költségeket.
Jelentősen csökkenti a folyékony hűtőrendszer építésének költségeit, lehetővé téve az autóipari radiátorok használatát a fűtőberendezésből és az akváriumból vagy a szökőkút szivattyújából. Egy ilyen réz radiátor, amely két ventilátort 120 mm-re fúj be, körülbelül 1000-1200 rubelt fog költeni, az alumínium változatot - körülbelül 600 rubelt. szivattyú - 600-1000 rubel mennyiségben. Azonban a legfontosabb részlet - a vízcsap.
A nagy teljesítményű modellek több mint ötven euróba kerülnek. Ráadásul rendszerint csak online áruházakban vásárolhatják meg őket, ami bizonyos nehézségekkel jár a feltöltés és a szállítás terén is (különösen országunk méretének megfelelően).
Az egyetlen módja ennek a helyzetnek a megoldása, hogy önállóan hozzon létre egy vízzárót. A maróberendezéssel ez csak technika kérdése. Ennek eredményeképpen vízhiányt kapsz, ami nem gyengébb a gyárban. A teljesítmény függ az alkotó által választott designtól. Sajnos azonban nem mindenki, aki olcsó hűtési rendszerrel kíván rendelkezni, hozzáférhet az ilyen berendezésekhez. És úgy tűnik, hogy nincs kiút. Ebben az esetben azonban milyen lenne ilyen hosszú bevezetés?
Valójában van egy kijárat, és az alábbiakban ismertetjük a víz nélküli blokk létrehozását a speciális berendezések nélkül.
Tehát az első dolog a gyártás előtt gondosan kiszámítani az összes méretet, meghatározni a vízblokk és a szerszám kialakítását.
Miután tanulmányozta a szerkezet a kész vízben blokkok, az elméleti alapjait hő- és áramlástan, valamint a józan ész, én választottam a fajta vizes blokk pin egy rombusz alakú keresztmetszete csapokat. Az alapot úgy döntötték, hogy vastagsága 5 mm, a magasság a csapok - 8 mm. Az alakja és mérete a csapok Miután sok gondolkodás úgy döntöttek, hogy tegye a következőket: az oldalán a rúd 4 mm, propil között csapok 2 mm-rel kisebb szög a sorrendben harminc fok cukorka. Természetesen jó anyag megteremtéséhez megfelelő anyagok szükségesek, így a választás egy henger alakú, 60 mm keresztmetszetű rézlemezre esett. A réz a legjobb fém a hővezető képesség és az ár arányában. Az eszköz lesz szükségünk: egy satu, fémfűrész (fő eszköze), Dremel és vágókorongok nagy átmérőjű, egy sor fúrók, fájlokat vagy (nincsenek különleges követelmények az űrlap nem szükséges), csiszolópapírral különböző kukoricadara, egy forrasztópáka, az olajozó olajjal, vonalzó, ceruza vagy vékony marker.
Annak érdekében, hogy a kívánt méretű munkadarabot meg lehessen látni, jelölje meg egy vonalzó pontot a szélétől a meghatározott távolságra, folyamatosan forgassa a munkadarabot. Ennek eredményeképpen ugyanazon a távolságon belül vannak pontok a széltől, majd egyszerűen csatlakoztassuk őket egy markerhez. A kapott vonal a vágási vonal.
Ezután szorítsa meg a munkadarabot egy csavarba.
Munkadarab a porban
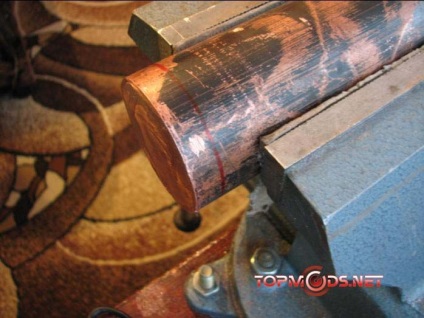
Annak érdekében, hogy a munkadarabon ne legyenek jelek az alsó pofájából, vastag kartonpapírbetéteket használtam. Majdnem minden munkát elvégezték a használatukkal, mert az esztétikai elemem számomra is fontos volt.
A munkadarab elfordításával el kell kezdeni a fűrészelést úgy, hogy a fűrész lánc nélkül legyen, és a munkadarab minden részében egyenlő vastagságú legyen. Úgy döntöttek, hogy a munkadarabot 14 mm vastagságban látják el. Ez a művelet körülbelül fél órát vett igénybe.
Fontos részlet az olaj, amelyet le kell csöpögtetni a vágás helyére, amikor a fémfűrész 3 mm-nél mélyebb mélységbe kezdett. Ez nagyban megkönnyíti a fűrészelést, mivel az olaj jelentősen csökkenti a súrlódási erőket.
A következő lépés a csapok gyártása. Ehhez le kell vágnia a jövő radiátort a réz tömbről. Ezt egy fémfűrész is elvégzi. Korábban, miután felvázoltuk a jövő radiátor munkaterületének határait, láttuk a felesleges széleket.
A felesleges anyag eltávolítása az oldalról
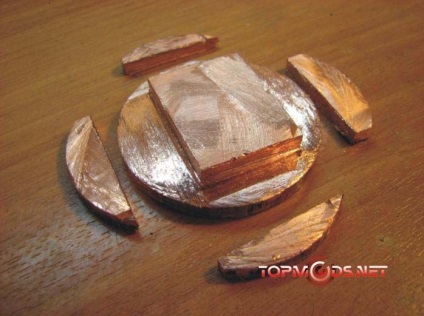
A csapok gyártási folyamata három szakaszból áll. Kezdetben a jövőbeli vágásokat egy dremel-del jelöljük. Ez azért szükséges, hogy megkönnyítsék a fűrészelést fűrészlapon. Szerettem volna egy vágófűrészt használni a vágáshoz, mivel gyorsabb, csendesebb és olcsóbb megoldásnak bizonyult. A fűrészelés során az olajat is csepegtetjük (régi 5 ml-es fecskendőt és motorolajat használtam).
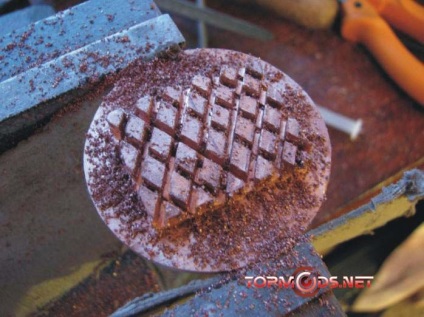
A végső szakaszban újra foglalkozunk a dremelrel, mivel technikailag nagyon nehéz a vágásokat egy fémfűrésszel végezni. Sokkal kényelmesebb a kellően nagy átmérőjű körök használata. 45 mm-es köröket használtam, 125 mm-es átmérőjű vágólemezektől függetlenül. A mélyebb vágásoknak nagyon óvatosnak kell lenniük. A réz nagyon viszkózus fém, így a dremel akár maximális teljesítmény mellett is elég egyszerű. Ez vezethet a dremel motor túlmelegedéséhez vagy a fúvóka károsodásához.
A kapott bázis kissé keménynek látszik, feldolgozható egy körömfájllal, hogy eltávolítsa az összes sorját és éles sarkát, amit később tettem.
Billets, miután a dremel-tel mélyítették a darabokat
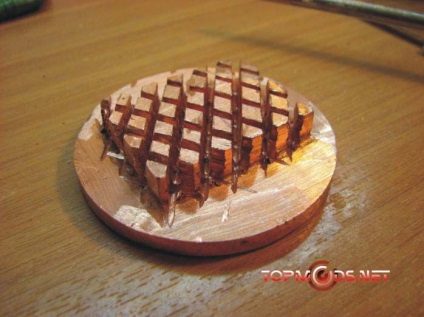
Lemezrézzel, sárgaréz vagy rozsdamentes acéllemezzel könnyen össze lehet hegeszteni a vízfelület fedelét. De akkor lenne osztatlan. Ezenkívül az ilyen anyagokat nem találták eladásra. Ezért úgy döntöttek, hogy két műanyag gyűrű és egy 1,2 mm vastag acéllemez fedelét készítik. És hogy az acél nem rozsdás, azt tervezték, hogy zaludit egy forrasztópálca.
A gyűrűk esetében a műanyag vastagsága 4,5 mm volt. Természetesen ebben az esetben kívánatos egy vastag lap használata, de ezt nem sikerült megtalálni, ezért úgy döntöttek, hogy két gyűrűt készítenek. A lapon egy 60 mm átmérőjű kört jelöltem meg. Ezt követően két négyzetet vágtak egy nagydarabból, az oldaluk pedig 60 mm-t is. Az üregek középpontjaiban fúrtak lyukakat, annak érdekében, hogy egy csavarral meghúzzák őket, majd együtt dolgozzanak. Fém fémfűrész segítségével két kört vágtam ki közülük.
Az üregeket egy csavarral meghúzzuk és összeszereljük
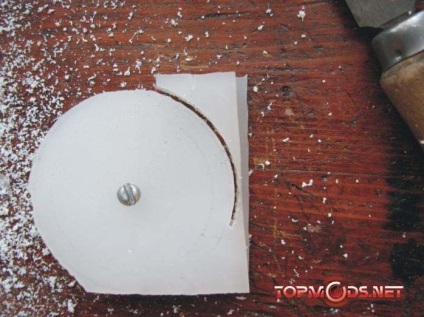
A belső rész eltávolításához a furat peremén fúrunk, és óvatosan vágjuk a kereszttartókat a nadfile segítségével.
Az acéllemezből dremel segítségével kivágtunk egy 60 mm átmérőjű kört. Fúrjon lyukat a vízblokkban és a fedél részleteit. Mindent összeszereltünk az M5 csavarok segítségével, és ezeket összeszereltük, hogy minden alkatrész azonos méretű legyen. A fájlból származó durva jelek kiküszöböléséhez 320-as szemcseméretű csiszolópapírt használtam.
Húzzuk össze a vízblokk részleteit, és szintre kerüljük az ellenséget
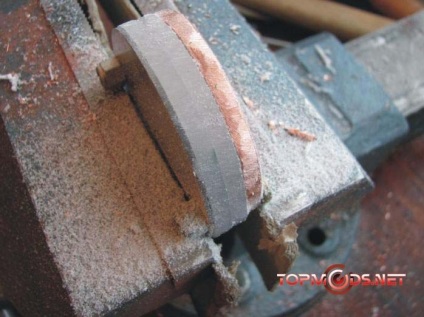
Szinte tökéletesen talp a talajon
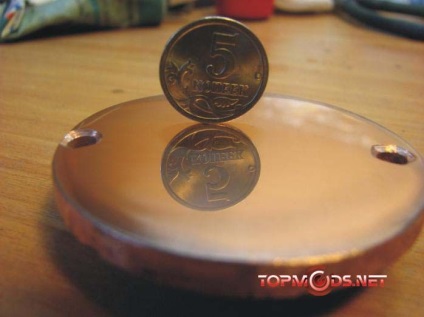
Egy fontos pont a fúrás, a bázis, hogy a csavarfejek kell teljesen áthatolnak egy anyagot, mivel a korszerű alaplapok gyakran tapasztalt kondenzátorok azonos magasságú és felszíni processzor elhelyezve kellően közel legyen a foglalat. A kinyúló csavarok károsíthatják őket a vízcsap telepítésekor. Annak érdekében, hogy teljesen elmozdulhassanak, a csavarokat csavaros fejekkel kell használni, és alátámasztani a hornyokat egy nagyobb fúró segítségével. Különösen 8 mm átmérőjű fúrót használtam.
Végül készen állnak a vízcsap minden része!
A vízblokk kész részei
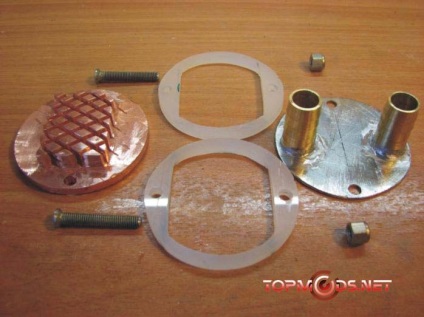
A következő lépés egy szorítólemez gyártása volt, amely nélkül a vízblokk használhatatlan. A meditáció és a vázlatok háromszorosával meghatározták annak alakját. Anyagként úgy döntöttek, hogy 2,5 mm vastag alumíniumlemezt használnak, mivel gyakorlatilag nem vonatkozik a deformációra, ami nagyon fontos a nyomólemezen. A processzorhűtőből származó szabványos többcirkulációs lemez segítségével terveztek lyukakat a lapon. Ezután az iránytű, a vonalzó és a marker használatával körvonalazódott a jövő részének vázlata.
Alumíniumlemez jelölés
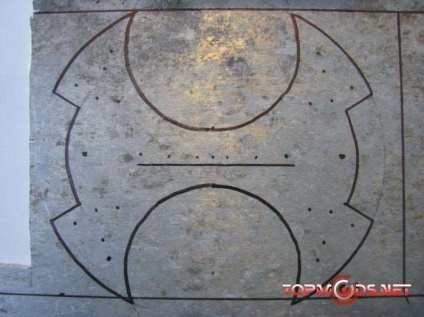
Fém fémfűrész segítségével vágták le. Ezenkívül a munkadarab felesleges sarkát vágták. Eltávolításához a belső részek a lemezen készült darabok, hogy azt a maximális mélységet, majd a kerülete mentén, ahol egy fémfűrész nem lehetséges, a fúrófej 5 mm volt nasverleno szükséges lyukak száma. Fúrásuk alumíniumban nem olyan egyszerű, mint amilyennek látszik. Annak ellenére, hogy a fúrási helyek korábban tervezték a mag segítségével, a fúró a folyamat gyakran oldalra. Ezért először 4 mm-es fúrólyukkal fúrtam ki a lyukakat, és a korrekció után 5 mm-es fúrót fúrtak. Ezután a felesleges részeket megtörték a fogók segítségével.
A felesleges anyag eltávolítása
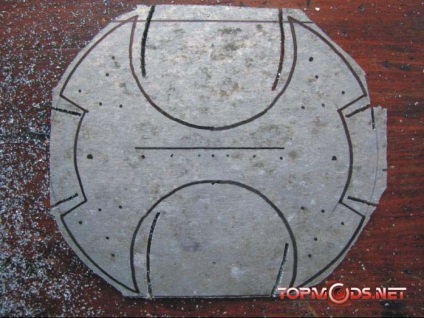
Fúrási furatok a kontúron
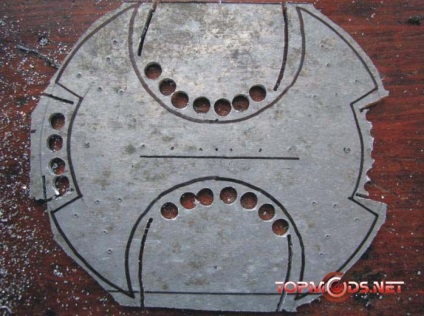
Miután levágta az alumínium felesleget fogókkal
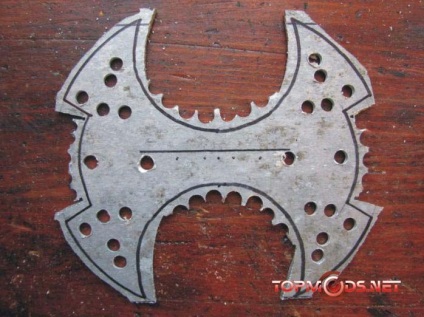
A következő szakasz a legnehezebb és legigényesebb. A fájl segítségével extra fém lerázható, és a kontúrok megközelítik a lemez tervezett határait. A munka során alapvetően egy lapos fájlt használtam, és a félkör alakú görbe határok feldolgozásakor. Annak érdekében, hogy eltávolítsam a sávokat és jeleket a fájlból, ugyanazt a csiszolópapírt használtam. Az eredmény egy olyan lemez, amely minden modern platformra illeszkedik, és hasonlít a sárgaréz csülökre a Lineage II játékból.
