Elérésére alkalmas módszerek a tervezett minőség és megbízhatóság
A tizenkettedik ciklusban cikk „Alapok és Technika Boundary Scan tervezés tesztelhető” áttekintést nyújt a rendszer hardver ONTAP cég Flynn Systems szánt párzás JTAG-PP és a vizsgálati csomópontokat.
A tervezett szintű minőséget és megbízhatóságot a termékek határozzák meg a mértékét és a becsült maximális értéke javítások, amelyek tartanak a szavatossági idő, attól függően, hogy a vásárlók igényeinek, a működési feltételek a termékek és azok megfelelő stratégia.
Ha a fogyasztó a szerződésben a kínálat 10 ezer. Eszközök megköveteli, hogy a szavatossági idő 10 év, a földrajz használat alkalmazza a teljes Oroszország területén, és a javítás várható el a gyártó saját, könnyen kiszámítható, hogy a hiba 1% Meg kell, hogy 100 utazó garanciális javítást.
A költségeket a garanciális javítást tervezett, általában szinten 2-4% az eladási ár. Ha az eszköz ér 100 ezer. Dörzsöljük. elvégzése javítási valamennyi fél a 3 millió. rubelt lehet ütemezni. Ez azt jelenti, hogy átlagosan egy út lehet töltött 30 ezer. Dörzsöljük. Ha a fenti berendezések fogják működtetni főleg Nyugat-Szibéria és a Távol-Keleten, a tervezett források nem lesznek elegendőek. Ha a készülékek 10 ezer. Dörzsöljük. és a párt - 100 ezer darab .. A helyzetet súlyosbítja óta jelentősen tervezett költségeket garanciális javítások növeli tízszeresére, és meghaladhatja a tervezett szintű nyereség. Növekvő eladási árak ellensúlyozni ezeket a költségeket csökkenteni fogja a versenyképességét a termékek, és akadálya lehet jövedelmező szerződéseket. Tekintettel a fentiekre, nyilvánvaló, leggyakrabban előforduló értéke a tervezett szintet hibáját: 0,1% vagy 1000 ppm.
Származó adatok felhasználásával a fenti példák, próbálja számítani a maximális javítási költségek a termelési folyamat során. Ha a szerkezet az egységár (100 ezer. Rub.) Gain 20%, a költség egyenlő 80 ezer. Rub. A költségek szerkezetét a komponensek, tartozékok és anyagok tartalmaznak 70% (tipikus érték gyártásához elektronikus eszközök), és a munka - 30% (24-é ..). Tegyük fel, hogy a készülék egyetlen fórumon design elemek 1000 és 3000 forrasztott kötések. Amikor az első osztályú szerelvény felszerelése az elérhető legmagasabb szintű hibák 100 ppm a közepén egy nagy párt. Ebben az esetben a 10 ezer. Darab a játékban. kapunk egy nyomtatott áramköri szerelvények:
3, 000 · 10000 · 100/1 000 000 = 3 000 potenciálisan hibás forrasztott kötés.
Első osztályú elektronikai alkatrészek beszállítók és a gyártók garantálják hiba mértéke 10 ppm. Ez azt jelenti, hogy 10 ezer. Darab a játékban. kapjuk:
1000 · 10000 · 10/1 000 000 = 100 potenciálisan hibás komponensek, azaz a 31% forrasztott szerelt nyomtatott áramköri lemez lesz az esetleges hibák.
diagnózis idejét és helyét a hiba az elektronikus modul, amely 1000 alkatrészek, átlagosan nem kevesebb, mint 4 óra. Abban az átlagos munkaköltség alkalommal magasan képzett szakember $ 25 US (beleértve az általános költségeket), a javítási költségeket, ha kibocsátó fél eszközök nélkül, az automatikusan diagnózis és lokalizációs hibák lesznek:
3 100 · 4 × 25 = 310 $ 000 vagy körülbelül 10 millió.
Az átlagos legkisebb javítási költség az eszköz lesz: 10 000 000/10 000 = 1 000 rubelt. Mint a második, a számítások érvényes, ha az összes nyomtatási egységet kell feldolgozni egy tételt, mert elején és végén a játék szintjén hibák rendszerint többszöröse (a játék elején el kell távolítani a következményei az emberi hibák és a nem megfelelő használata az alkatrészek és kiegészítők, valamint a végén - a következmények hiánya alkatrészek). Ezen kívül még a szakemberre / légiforgalmi irányító és a legkomolyabb felügyelők nem engedheti meg magának, hogy teljes mértékben ellenőrizni a termékek megfelelnek a tervezési és szabályozási dokumentációt. Ennek eredményeként - további költségek javítási eszközök sikertelenül átvételi tesztek és a fogyasztó a jótállási idő alatt.
A fenti példák egyértelműen megerősítik a jól ismert posztulátum „helyreállításának költségeit a hiba kisebb, közelebb a előfordulási helye a potenciális jegyezte”, és ez azt jelenti, hogy meg kell keresni a termelés minőségi és megbízható termékek a gyárban.
A második kérdés: milyen technológiával éri el a tervezett szintet minőség és a megbízhatóság, és milyen költségeket kell ehhez? Tehát, már meghatározott cél: hogy dolgozzon ki és hajtsanak végre olyan technológia, amely a tervek (számított) szintű minőség és a megbízhatóság a termékek minimális (optimális) költség.
Vegyünk egy példát: ent-TII beágyazott jellemző gyártási folyamat a szerelt nyomtatott áramköri lemez szerelési (lásd 1. ábra ..).
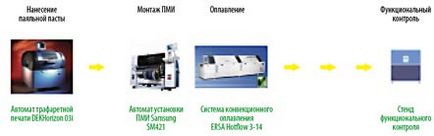
Ábra. 1. Technológiai folyamat az összeszerelés nyomtatott áramköri összeállítások nélküli ellenőrzési és felügyeleti rendszerek
Miután bevezetése rendszer AOI minőségellenőrzési forrasztott kötések szerelési és hibák társított termékek egy offset komponenst vezet képest érintkező felületeket az áramköri lapon, jelentősen csökkent. Összhangban a javasolt algoritmus (lásd. Ábra. 2) vett konverziós diagnosztizálására és lokalizálására említett típusú hibák kielégítőnek tekinthető.
2. táblázat minőségi kritériumok felületszerelt alkatrész összeszerelés követelményeinek megfelelően a különböző szabványok
Defect - 1. osztályú, 2. Az oldalirányú elmozdulás (A) meghaladja az 50% az érintkező felület szélessége (W), vagy 50% -a a szélessége a érintkezőpárna (P) (kiválasztott minimális érték).
Hibák - 3. osztály.
Az oldalirányú elmozdulás (A) meghaladja a 25% az érintkező felület szélessége (W), vagy 25% -a a szélessége a érintkezőpárna (P) (kiválasztott minimális érték).
Defect - 1. osztályú, 2. Az oldalirányú elmozdulás (A) meghaladja az 50% az érintkező felület szélessége (W), vagy 50% -a a szélessége a érintkezőpárna (P) (kiválasztott minimális érték).
Hibák - 3. osztály.
Az oldalirányú elmozdulás (A) meghaladja a 25% az érintkező felület szélessége (W), vagy 25% -a a szélessége a érintkezőpárna (P) (kiválasztott minimális érték).
o. 10.7 (ábra. 50) Defect "oldalirányú elmozdulása" (A) 10% -kal meghaladja az érintkezési felület szélessége (W).
Defect - 1. osztályú, 2. A maximális oldalirányú elmozdulását (a) meghaladja az 50% -át a szélessége a kimenet (W), illetve 0,5 mm-es (a kisebb érték van kiválasztva).
Defect - 1. osztályú, 2. A maximális oldalirányú elmozdulását (a) meghaladja az 50% -át a szélessége a kimenet (W), illetve 0,5 mm-es (a kisebb érték van kiválasztva).
Defect "maximális oldalirányú elmozdulás" (A) meghaladja a 25% a kimenet szélessége (W).
Defect - osztály 3. A maximális oldalirányú elmozdulás (A) meghaladja a 25% -át a szélessége a kimenet (W), illetve 0,5 mm-es (a kisebb érték van kiválasztva).
Defect - osztály 3. A maximális oldalirányú elmozdulás (A) meghaladja a 25% -át a szélessége a kimenet (W), illetve 0,5 mm-es (a kisebb érték van kiválasztva).
A következő legnagyobb hiba típusa „beállítása nem megfelelő komponens” (3 sor a 2. táblázatban és a 2. ábrán). A legvalószínűbb oka a nem megfelelő telepítés összetevők lehetnek:
- üzemzavar a feeder felszerelés;
- hibás alkatrész (házasságot gyártó);
- kár, hogy a komponens a gyártási folyamat (folyamat hiba).
A leghatékonyabb eszköze a diagnózis és lokalizációja hibák Az ilyen típusú automatikus in-áramkör vezérlő. Tekintettel a nagy sűrűségű szerelés termékek és azok széleskörű in SPEA4060 rendszer (lásd. Ábra. 4) választottuk, mint egy eszközt az automatikus in-áramkör elektromos vezérlés.
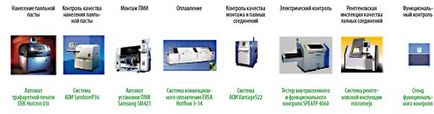
Ábra. 4. folyamatábra nyomtatott áramköri szerelvények végrehajtásában modern automatikus ellenőrző és szabályozó rendszer
Miután a bevezetése automatikus áramköri SPEA 4060 vezérlő a hibák száma társított termékek a telepítés a hibás alkatrész jelentősen csökken. Összhangban a javasolt algoritmus (lásd. Ábra. 2) való átalakítására a vett diagnózis és lokalizációja hibák a fent említett típusú kielégítőnek tekinthető.
A következő legfontosabb típusa a hiba - „elegendő mennyiségű forrasztószer a forrasztott kötések” (4 sor az 1. táblázat és a 3. ábra). A legvalószínűbb oka az elégtelen mennyiségű forraszanyag lehet:
- megfelelő méretű párna (konstruktív Tóra hiba);
- megfelelő méretű nyílás (a tervező hiba);
- rossz minőségű stencil (szita hiba producer);
- rossz minőségű forrasztó paszta (hiba szállító és / vagy a gyártónak);
- rossz minőségű forraszpaszta a munka (az eljárás hibája);
- hibás képernyő nyomtató beállításokat (mozgási sebességét és / vagy a nyomás a doktor blade);
- csavarás a PCB.
Hibák tervezők azonosítani kell a szakaszában elfogadásának a tervdokumentáció, a technológiai gyártás-előkészítési és gyártási prototípusok - mielőtt színpadra termékek tömegtermelése. A minőség a stencil, forrasztópaszták és nyomtatott áramköri lapok kell vezérelni egy bemeneti ellenőrzés.
Minőségi forrasztópaszta különböző alkalmazások által szabályozott a vonatkozó előírásoknak (lásd. Táblázat. 3.).
3. táblázat kritériumai átvételi minőség forraszpaszta szerint a NASA-STD-8739
A pasztát kell alkalmazni a pontos nyilvántartás a érintkező felületeket, és van egy egyenletes vastagságú. Anélkül, hidak, buborékok, hegek és a kenést.
A NASA-STD-8739,2 [8,2], [8,6]
hidak Oktatás - jelzi a hibás folyamat paramétereinek forrasztó paszta.
A NASA-STD-8739,2 [8.7.4.f], [12.6.1.a.1]