Mi Lean
Kedves Gemba Coach,
Küzdök, hogy megértsék, mit ember jelent „rendszer Ling” (a rendszer lean termelés)?
Egyértelmű! „System” - e szavak valamelyikével, valamint a kultúra, amelyek jelentőséggel bírnak az egyes ember, aki használja azt, de ezek egyike sem érték nem pontosan olyan, mint - hogy zavaró. „Rendszer” a menyhal használják számos nagyon különböző értékeket, és különösen a szót hozzátéve, hogy zavart, nem pedig tisztázása, hogy mi történik.
Kezdve a hivatalos meghatározás, utunkat egy baj? „Rendszer” két alapvető meghatározások:
- A gyűjtemény elemek együtt dolgoznak részeként egy kölcsönhatásba lépő mechanizmus vagy hálózathoz; egészt, amely nagyobb, mint a részek összessége.
- Egy sor elvek vagy szabályok, amelyek szerint valami történik; szervezett rendszert vagy módszert.
Vagy szisztemikus gondolkodók meghatározás Donella Meadows:
* System - egy sor egymással összefüggő elemek koherens megszervezni oly módon, hogy elérjen valamit. Ha van egy percig gondolkodni, akkor látni fogja, hogy a definíció rendszer kell állnia a következő dolgokat: elemek, kapcsolatok, valamint a beosztás vagy a célra.
A legkorábbi említés a „rendszer” Lin, akivel találkoztam - a fordítási Art Smolli (Art Smalley) japán Tayiti Ono előszót az első kiadvány, a Toyota termelési rendszer:
„TPS (Toyota Production System) egy sor egymással összefüggő tevékenységek megszüntetését célzó mudy veszteségek csökkentése, a minőség javítására és a termelékenység növelése.”
Ez a „rendszer” különbözőképpen értelmezik. Az első napokban a másolás Toyota autóipari vezetők gondolt a Toyota termelési rendszer, mint egy sor termelési eljárások, hogy jobb teljesítményt. Ezek alapvető gondolkodás volt - ha másolt, ami a Toyota, akkor ugyanazt az eredményt kap. Például nagyon jól emlékszem a növény, amelynek célja az volt, hogy szimulálja a pontos előírások Toyota, forgalomba nagyon kevés helyet anyagok, felszerelések és kiegészítők. Mivel a folyamatok nem működnek szinten a folyamatok Toyota termékek, amelyek remade, tele mindent, és ez egy teljesen sikertelen volt.
Ezután Stiven Spir és Kent Bowen (Steven Spear és Kent Bowen) írt egy nagyon befolyásos cikk „dekódolása DNS Toyota Production System” címmel, amelyben azt javasolta, hogy a TPS alapul szabályrendszer:
- 1. szabály: Minden munkát kell nagyon pontosan meghatározni tartalmával kapcsolatban, sorozat, az időzítés, és az eredményeket.
- Szabály # 2: Minden vevő-szállító kapcsolat szükséges közvetlen, egyértelműnek kell lennie megválasztásának kritériuma az igen-nem, mikor kérések küldésére és fogadására válaszok.
- Szabály # 3: A pálya mozgásának egyes termék vagy szolgáltatás egyszerűnek kell lennie, és irányítsa.
- Szabály # 4: Minden javulás kell tenni összhangban a tudományos módszer. irányítása alatt a tanár, a legkisebb mértékben lehetséges, a szervezeti szint.
Annak ellenére, hogy egy meglehetősen találó leírása a része ennek a megközelítésnek bizonyult elég tehetetlen játszani gondolkodás Toyota mivel ösztönözni mechanisztikus gondolkodás és a megértés a „szabályok”, amelyek olyan erős a nyugati gondolkodásban, míg a Toyota ragadt sokkal „szerves” látás „rendszer gondolkodó ember „(” az emberek gondolkodás rendszer „). Veterans mondta, a Toyota vezetői, a TPS valóban a módszer arra kényszeríti az embereket, hogy ahelyett, árukapcsolás őket szigorú szabályok.
Amint az eszközöket válik több jól ismert, van egy másik értelmezés, amely egyike a „rendszer”, olyan módszereket alkalmaz, amelyek követik a legszigorúbban. Ez a változat kezdődött azzal a megközelítéssel, a „modell-sejt”, és hogyan osztja ezeket sejtmodeiiekre az egész vállalkozás létrehozása révén „kormányzás” support „rendszer”. Talán a legjobb mutatója a rendszer megközelítés menedzsment Dzhon tussen (John Toussaint), aki gyakorolja ling . a kórházak, a legnagyobb struktúrák, amit csak elképzelni az ő nagyszerű könyv „hasznosítás irányítás” (irányítás javulóban), ő határozza meg a saját elképzelés a rendszer:
- A modell-sejt - megmutatni a többi szervezet, hogyan és mit lehet tenni, és terjesztésére eszközöket.
- Szervezetre kiterjedő értékeket és elveket, amely végigvezeti a munkát.
- A központi iroda segítség és támogatás (A központi promóciós iroda).
- A rendszer kezelése, a fejlett, hogy az élen, a vezető alapmű.
- A spread (standard) dolgoznak a rendszeren keresztül.
- A szerkezetátalakítás a többi szervezet, emberek, politika, és gyakorlatok a szervezet, amely támogatni fogja ezt a munkát.
Ez is egy nagyon erős megközelítés, de aztán megint, elvezet minket egy nagyon mechanisztikus gondolkodás és a megértés a „rendszer”, míg a Toyota professzor szerint Takeuchi (Takeuchi), látja magát, mint egy „zöld paradicsom”, amely folyamatosan fejlődik, de soha érlelődik:
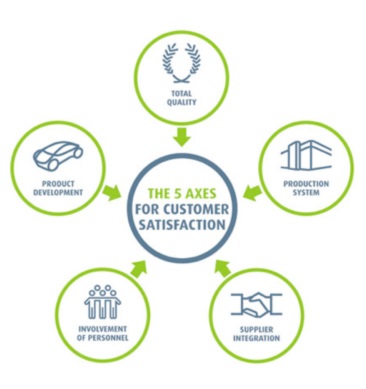
1.Total Minőség - Total Quality; 2. Termelési rendszer - a termelés; 3. Szállító Integráció - Integráció szolgáltatók 4. bevonása Personnel - bevonása személyzet 5. A termék fejlesztés - (javulás) termékek A központban: Az 5 tengelyei Customer Satisfaction - 5 tengelyes rendszer az ügyfél-elégedettség.
Ezután a Sommer-Allibert Excellence rendszer (rendsterfejlesztést Sommer-Allibert)
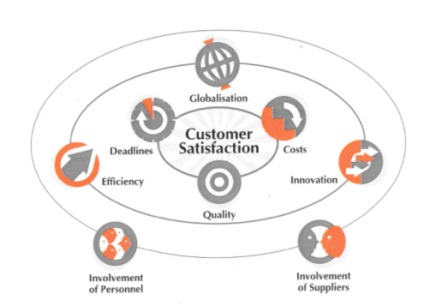
Külső pályára: 1. bevonása Ellátó - a szállítók bevonása; 2. bevonása Personnel - bevonása személyzet. Átlagos pályára: 1. Globalizáció - Globalizáció; 2. Innováció - Innováció; Hatékonyság - Hatékonyság. A belső pályán: 1. A költségek - költség; 2. Minőség - Minőségi; 3. Határidők - Határidők. A központban - a vevői elégedettséget.
És akkor a Faurecia Excellence Rendszer (Fores Improvement System) (Fores lenyelt Allibert)
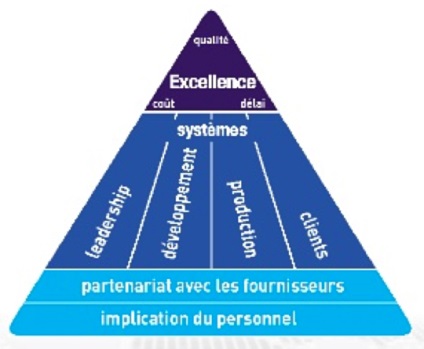
Az alapja a piramis: 1. A bevonása személyzet; 2. Partnerség a beszállítókkal. A közepén a piramis: 1. Vezetés; 2. Fejlesztési; 3. Termelési; 5. Az ügyfelek. A piramis csúcsán: 1. Minőségi; 2. Költség; 3. késések.
Rendszer, amely ma is, évtizedekkel később. Mit gondolt, mindhárom esetben volt a legfontosabb kihívások. amellyel a vállalat kénytelen volt szembenézni. Sok szempontból a „rendszer” illeszkednek a meghatározása egy sor egymással összefüggő eszközök, valamint minden irányítási rendszert.
Mi meghiúsítja az apám a mai napig, ez nem az, ami volt beállítva, hogy nem. Tanulás Toyota 1975 óta, és saját „aha!” kiemeli előrelépés Toyota gyárak és műszaki részlegek Freddie megértsék a rendszer, mint egy sor, egymással összefüggő „tipikus problémák / tipikus megoldásokat.”
Minden folyamatnak van legalább egy nagy miskontseptsiyu amely csökkenti annak hatékonyságát. Az első napokban, a Valeo (Valeo), a két legnagyobb miskontseptsii vezet a gazdaságtalan termelés sejtek:
- Emberek, gépek, anyagok, eljárások (variáció őket) instabilitást az áramlás részei, és lehetetlenné tette, hogy összehangolják a munkát a falon.
- Nagy tételekben túlterheltek folyamatok anyagokat.
Freddy rendre oszlik ( „osztályok készségek threading és elhelyezése” ( „flow és az elrendezés műhelyek”) minden növény, valamint a tanulmányok SMED. A fejek, a gyárak és a központi vállalati csapatok kifejlesztett egy sor az eljárások és gyakorlatok, hogy elérjék a kívánt eredményt. És ez volt a bürokrácia is.
Egy véletlen folyamatok a tapasztalatok Valeo termelési rendszer vált mindenütt jelen „menetrend”. Egy bizonyos ponton, megzavar az eltérő tanulási és tanulságok, amelyeket szerezte együttműködve a Toyota és a gyakori utazások szállítóinak Toyota Japánban, Freddie és a tanácsadó jött a kétdimenziós módszer előrehaladását mutatja:
- érettségi szint 0 = nincs 5 = tökéletesség.
- Lin, a téma a téma.
A kapott utcatérképek (az egész mappa őket), érdekes volt, hogy összegyűjtse, mint strukturált tanulási görbe Valeo azonban, hogy a csalódás Freddy, megfordult teljesen haszontalan, ahelyett, hogy lesz egy telepítési program minden növény. Oktatás, kiderül, egy egyéni tapasztalat, és bár a vezetők el lehet küldeni sensei, nincs közös módon tanulni. Az oktatás továbbra is teljesen helyzeti, körülményeitől függ a földön, és emberi módon, hogy „aha!” időben, egy bizonyos gyakorlat különböző eszközöket, speciális körülmények között. Ez egyébként nem akadályozta meg a cég, hogy hozzon létre egy végtelen úton térképek irányítani a ling-transzformációk (sikertelenül), és soha bevallja, hogy erősítsék a bürokratikus szempontból a „rendszer” helyett bátorítják a kaizen.
Freddie mindig is úgy, hogy szükség van egy bizonyos mennyiségű bürokrácia, hogy tartsák be a vonatkozó elképzelések (a bürokrácia most hívja a „rendszer”), bosszantotta sokan vezetők, akik végre minden alaki nélkül megértéséhez meg kell fontolni „tipikus problémák / szabványos megoldások” növelni a termelékenységet és a munka hatékonyabbá tétele.
Tehát ez lenne az én meghatározása „Lean” - egy sor közös problémák / tipikus ellenintézkedéseket lehet rituális „lin-eszközök”, de ahol mindenkinek meg kell keresni egy adott ellensúlyozása saját helyzetüket, saját Gemba elérni mind növekedése termelékenység, és jobban megértsék az endemikus (jellemző) a probléma. „Rendszer” része az, hogy amit elért, akkor kap egy megértését két dolgot:
- Az Ön listája tipikus problémák növekvő egyetlen kérdés egy időben, a katalógus konkrét ellenintézkedések (különböző) más feltételekkel.
- Elkezdi, hogy milyen mélyen összefüggenek tipikus probléma, ahogy közeledik a valódi okát.
Mi van ma? Az összes különböző kísérletek, hogy olyan rendszert hozzon létre lean gyártás, a legjobb, hogy tudom - az átalakulás Boutilonnom John (John Bouthillon) saját építőipari vállalat - az itt leírt saját szavaival.
Butylone megoldotta az egyik probléma a másik után, ötleteket merítenek a példa a Toyota termelési rendszer, ami eszközök a tanulmányi problémák mindegyikére csapata, az egyes site: