Forrasztás vákuumban és redukáló atmoszférában - forrasztás indukciós fűtéssel
Forrasztás vákuumban és redukáló atmoszférában
Ha a fém normál körülmények között magas hőmérsékletre hevít, az oxigén a levegőben oxidálja a felületét, és így képződik. Az oxidok jelenléte megnehezíti a forrasztási folyamat fenntartását. A levegő forrasztásakor a felület eltávolításához és tisztításához speciális fluxusokat kell használni. Azonban a fluxusokkal való forrasztás, amely lehetővé teszi az erős összeköttetést, nem nyújt védelmet az alkatrész teljes felületének az oxidációtól; így forrasztás után meg kell tisztítani az alkatrészeket a fluxustól és a méretaránytól. Ennek elkerülése érdekében a levegőben lévő fűtött termék szigetelésének módszereit alkalmazzák, lehetővé téve a nem oxidatív forrasztási folyamatokat. Ezek közé tartozik a forrasztás vákuumban és forrasztás csökkentő légkörben.
Forrasztás vákuumban. Mint említettük, a nagyfrekvenciás forrasztás egyik előnye a forraszthatóság vákuumban. A vákuumforrasztás előnye, hogy amikor olyan környezetben melegszik, ahol nincs oxigén, a fém oxidációja nem áll fenn, és magas színvonalú forrasztást igényel, nem szükséges fluxust használni. A megfelelő fűtési módban egy részegységben és egy bizonyos késleltetésnél biztos lehet benne, hogy a forrasztás minősége minden részre azonos lesz.
Az első vákuumos forrasztásra szolgáló eszköz egy kerek rézasztal volt, amelynek talajfelülete van, amelyen egy forrasztásra előkészített munkadarab telepíthető. A darabot egy üveg kupakkal borították, és csiszolt széleit az asztal felszínéhez szorosan illesztették. A jobb tömítés érdekében a tábla felületét technikai vazelinnel kenni lehetett. A levegőt a kupak alatt leeresztették az asztal nyílásán keresztül. Kb. 10 ~ 3 mm Hg-os folyadékkal. Art. amely néhány másodpercen belül elért, a rész forrasztásra kész.
Az üveg kupak felett elhelyezkedő induktor a generátor bekapcsolásakor nagy erősségű energiát továbbított a forrasztott részhez, mint a levegő forrasztása során. Egy ilyen primitív eszközön a laboratóriumban prof. VP Vologdin elvégezte az első kísérleteket a réz és az ezüst forraszanyagok alkatrészeinek és vágóeszközeinek forrasztására.
Valamivel később egy automata gépet is létrehoztak a belső égésű motorok gyújtógyertyák forrasztásához (1. A vízzel hűtött, masszív rézlemezrekesz speciális aljzatainál forrasztott részek voltak beépítve, amelyek tetején üvegkupakkal voltak bevonva. Az asztal elforgatásakor az újonnan beszerelt kupak alatt lévő helyet külön vákuumszivattyúkkal ellátott csatornarendszerrel csatlakoztatták, amely előzetes, majd mély vákuumot biztosított. A tábla részletekkel egy speciális meghajtórendszer segítségével periodikusan, rendszeres időközönként forgó mozgást hajtott végre, némi szögben. Bizonyos helyzetben a kupakot egy gyűrűs induktor fedte le, és egyidejűleg a generátort bekapcsolta. A rész azonnal beleivódott hozzá. Melegítés után a kívánt hőmérséklet és a forraszanyag tömböt megolvasztjuk induktor emelkedő, a melegítést kikapcsoljuk, és a táblázatot átkerült a következő helyzetbe, ami után a fűtés megindítása következő elemeket. Így az alkatrészek viszont az induktor felé közelítettek, ahol a forraszanyag olvasztásához és forrasztáshoz szükséges energia egy részét kapták. Fűtés után az alkatrészeket lehűtöttük, és a hőt átvittük egy rézasztalra, intenzíven vízzel hűtöttük. Végén a forrasztási helyet a kupak alatt egy ideig nem csatlakozik a környező levegő, mintha eltávolítani a kupakot, mielőtt az alkatrész hőmérsékletre hűtjük 100-150 ° C, a felületén oxidálódik és elsötétedik. A vákuumban lehűtött részletek fényes felületűek, mintha csak csiszolták volna őket. A részek forrasztása vákuumban rendkívül magas.
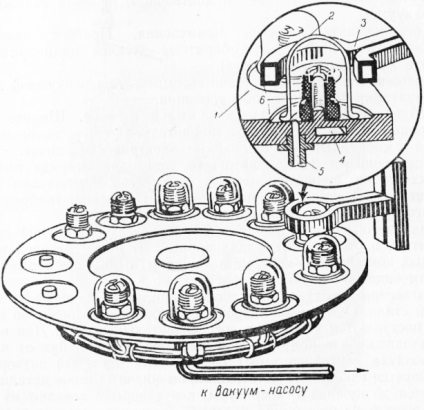
Ábra. 1. Gépi szerszám vákuum alkatrészek forrasztásához: 1 - réz asztal; 2 - üvegkupak; 3 - induktor; 4 csatorna az asztal vízhűtéséhez; 5 - a levegő szivattyúzására szolgáló csatorna; в - forrasztott alkatrészek
A nagyfrekvenciás forrasztás vákuumos folyamatának számos pozitív aspektusa ellenére alkalmazásának területe a mai napig nagyon korlátozott.
Az iparban való széles körű használatát megakadályozó okok miatt a következőket kell tulajdonítani:
1) viszonylag alacsony termelékenység a folyamat részek melegítésének köszönhetően és hosszú várakozási idő alatt;
2) korlátozott alkalmazási terület. Az eljárás elsősorban a kis méretű hengeres részek forrasztására szolgál tömegtermelésben;
3) a vákuumforrasztáshoz és a vákuumberendezés működtetéséhez használt automatikus gépek létrehozásának összetettsége.
Forrasztás csökkentett környezetben. A redukáló környezetben a speciálisan felszerelt elektromos kemencékben végzett rézforrás-eljárás széles körben ismert.
Ennek lényeges hiányosságai, számos pozitív tényező jelenlétében, a berendezések magas költsége és hiánya. A forrasztás során a kemencék hosszú melegítési és hűtési időt igényelnek.
Mivel a speciális kemencében redukáló hiányos tápközegben bizonyos esetekben termelnek forrasztás alkatrészek speciális tartályokban, amelyek betöltött hagyományos hőkezelő kemencék, amelyek magas hőmérsékleten.
A konténerek hőálló acélból készült dobozok. Ezek hegesztett csövek, amelyeken keresztül a forrasztás során a redukáló gázok belépnek és elhagyják. A tartályban levő részek elkülönítése a levegő oxigénből történő forrasztása során, a tartály speciális homokzárással van ellátva, vagy agyaggal van takarva. Miután az alkatrészeket felmelegítettük a kívánt hőmérsékletre, a tartályokat eltávolítottuk a sütőből és lehűtöttük, miközben a redukálóközeget addig folytattuk, amíg a részek le nem hűltek.
Ez a forrasztási módszer nagyon tökéletlen, mivel hosszú időbe telik, és nagyon kis mennyiségű részegységet enged a nagy energiafogyasztásnak.
A termelékenyebb folyamat nagyfrekvenciás árammal történő melegítéssel rendelkező forrásokban forrasztja (2. ábra). Ez a forrasztás faj csak hagyományosan lehet nevezni a nagyfrekvenciás, hiszen, ellentétben azzal, amit megfigyelt minden más módszer a magas frekvenciájú fűtés, itt áramok alig indukálódik a rész is, és a fűtött tartály, amely, amely viszont átviszi a hőt az elem keresztül a redukálóközeg hővezető képességét. Ugyanakkor a nagyfrekvenciás fűtés egyik előnye elveszett - az a képesség, hogy csak a kívánt részzónát felmelegedik.
A nagyfrekvenciás fűtésben lévő tartályokban lévő alkatrészek forrasztási ciklusa többször is csökkenthető a kemencék forrasztási ciklusához képest. Ez lehetővé teszi számunkra, hogy forraszanyagként ne csak réz, hanem sárgaréz is használható. A redukáló környezetben a forrasztás jelenlegi módszereivel a sárgaréz nem használható forraszként, mivel a hosszabb melegítés kedvezőtlenül befolyásolta tulajdonságait.
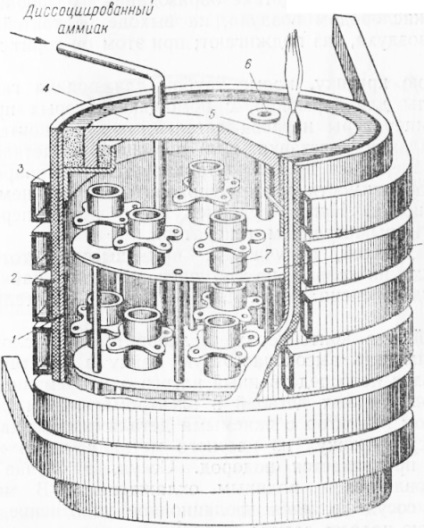
Ábra. 2. A tárolóedény diagramja nagyfrekvenciás keményforrasztáshoz egy redukáló környezetben az alkatrészek közvetett melegítésével: 1 - tartálytest; 2 réteg hőszigetelés; 3 - induktor; 4- konténer fedele; 5 - egy cső a redukálóközeg ellátására és eltávolítására; 6 - aljzat hőelemekhez; 7 - forrasztott rész; 8 - állni
A nagyfrekvenciás fűtéssel ellátott konténer hegesztéssel készül hőszigetelő acéllemezből, amely egy hőszigetelő talphoz van felszerelve. A tartályt több fordulatú induktorba helyezzük. Az induktor és a tartály között egy hőszigetelő réteget helyeznek el, hogy csökkentse a sugárzás energiaveszteségét. A tartály alját több hullámosítással készítik el, hogy megóvja a megsemmisítéstől a többszörös fűtés és hűtés során fellépő hőfeszültségek következtében. A felső masszív fedélen bevezetik és eltávolítják a gázokat, amelyek közül a legjobb a disszociált ammónia.
A tartály forrasztása és hűtése során a gáz folyamatosan áramlik. Annak érdekében, hogy kizárják a robbanás lehetőségét a helyiségben, mivel robbanásveszélyes hidrogén-keverék keletkezik levegő oxigénnel, a tartály kimenetén a levegő kiáramlása után a gáz meggyullad; míg sárgás lángot éget.
A felső fedélen, a gázellátó csöveken kívül, meg kell hegeszteni a hőelem-burkolatokat, amelyek segítségével az alkatrészek fűtési hőmérsékletét szabályozzák; A tartály aljára egy speciális állványt helyeznek az alkatrészek elhelyezésére. A tartályfalak felmelegítését mindig egy termoelem vezérli, amely szükség esetén vezérelheti a készülék be- és kikapcsolását. A fűtést leginkább a generátor be- és kikapcsolása időszakonként végezheti el.
A konténerek nagyfrekvenciás forrasztása által nyert alkatrészek minősége nem alacsonyabb a redukáló atmoszférában működő különleges kemencékben készült forrasztó alkatrészek minőségénél.
Továbbá forrasztás konténerek laboratóriumi usloviyh könnyen és egyszerűen alkalmazható nagyfrekvenciás keményforrasztó redukáló környezet segítségével közvetlen melegítés egyidejűleg egy vagy több, hasonló alkatrészeket az elektromágneses mezőben az induktor. Ebben az esetben a forrasztott részeket tartalmazó induktor egy speciális edénybe kerül - egy nem-vasfémből készült ház, amelyen forrasztás közben hidrogén halad át. Az edényt szükség esetén vízhűtéssel állítják elő. Helyett a bemeneti induktivitás egy tartályban van egy szigetelő tömítés, védelme a belső üreg a hajó a levegő behatolása, mint induktort a kapcsai. Az induktor alkatrészei egy lyukon keresztül vannak betöltve, amely a gáz átadása előtt hermetikusan lezárja a fedelet egy ellenőrzőablakkal (3. ábra).
A gázt ugyanúgy töltjük és kezeljük gázzal, mint a redukálóközeggel ellátott tartály forrasztásához. Az alkatrészek forrasztása során a fûtést az elhasznált üzemmódban kell végrehajtani bizonyos késleltetéssel, kísérletileg. A gázellátás leállása után a részeket 100-120 ° C alatti hőmérsékletre hűtjük, majd a következőket helyettesítjük. Ebben a folyamatban a hidrogén felhasználható, amelyet laboratóriumi körülmények között a Kipp-berendezésben nyerünk savas cink hatásával, majd tisztítjuk és eltávolítjuk a nedvességet. A gázáram és az edényben lévő nyomása elhanyagolható lehet, de elegendőnek kell lennie ahhoz, hogy folyamatosan fenntartsa a gáz égését a kimeneten. A kimeneti csövön üvegcsúcsra kell helyezni, töltve rézzel. Célja, hogy megakadályozza a hidrogén kitörését az edényben, és ezáltal biztonságos munkakörnyezetet biztosítson. A hidrogén redukálóközegként való jelentős hátránya, hogy képes robbanásveszélyes keverékeket képezni a levegő oxigénjével, amely nagy figyelmet igényel és pontosan betartja a hidrogén kezelésére vonatkozó utasításokat.
Alacsony termelékenység és korlátozott kapacitás ellenére az alkatrészek közvetlen melegítésével történő forrasztás sokkal tökéletesebb folyamat, mint a forrasztás a tartályokban lévő alkatrészek melegítésével.
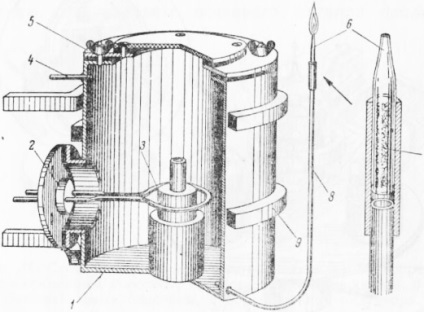
Ábra. 3. A nagyfrekvenciás keményforrasztáshoz használt berendezés diagramja redukáló környezetben, az alkatrészek közvetlen hevítésével: 1 - edény; 2 - szigetelési tömítés; 3 - forraszanyagú induktor; 4 - cső gázellátáshoz; 5 - a hajó fedele; 6 - biztonsági csúcs; 7 - rézcsípő; 8 - cső a gáz eltávolítására; 9 - hűtőcső
Sajnos eddig a részegységek nagyfrekvenciás forrasztása vákuumban és redukáló környezetben nem mutatkozott széles körben, bár ezek a folyamatok olyan progresszív technológiai folyamatok, amelyek nagy figyelmet érdemelnek.
Ilyen készülékeknél a forrasztást semleges gáz környezetben, például argonban is elvégezhetjük. Az argon megvédi az alkatrészeket a melegítés során az oxidációtól, kedvezőbb feltételeket teremt az alapfém forraszanyagának nedvesítéséhez és a résekbe áramlik. Kívánatos minimális mennyiségű szennyeződést, különösen oxigént tartalmazó argont használni. Az argon forrasztása jobb, mint a levegő forrasztása, de rosszabb, mint a hidrogén forrasztása, mivel bizonyos mennyiségű fluxust igényel, és kevésbé gyönyörű vegyületeket eredményez. Az argon sűrűbb, mint a levegő, nem ég és nem támogatja az égést, ezért kényelmesen kezelhető forrasztással. Könnyen forrasztható a kis részek argonja az üveg kupak alatt, ahogy azt vákuum forrasztása esetén is előállítják (4. Ezt a folyamatot célszerű alkalmazni, ha az alkatrészek belső üregekkel rendelkeznek, amelyek védelmet igényelnek a forrasztás során keletkező oxidációtól. Ebben az esetben a gázt el lehet látni egy speciális kapcsolóberendezésben, amely a forgóasztalon található, a forrasztott rész alatt lévő lyukon keresztül, majd az üveg kupakjának tetején lévő lábfejen keresztül.
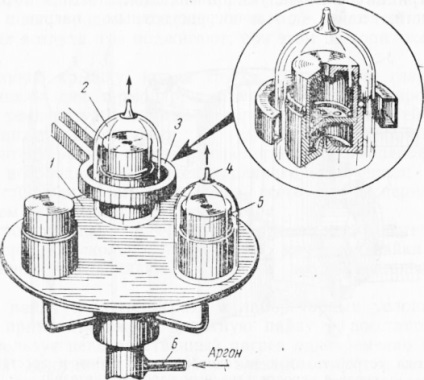
Ábra. 4. Az argon alkatrészek alkatrészeinek forrasztására szolgáló eszköz diagramja: 1 - rézasztal; 2 - üvegkupak; 3 - induktor; 4 - sapka sapka gázkiömléssel; 5 - forrasztott alkatrészek; 6 - cső gázmentesítéshez
Ugyanezek a célokból, ha valamilyen alkatrészeket forráznak a levegőben, az argon az oszlop belső üregén keresztül fújhat, például a felelős nagynyomású üzemanyagcsövek nagyfrekvenciás forrasztása során. Ha a munkakörülmények és az alkatrész felépítése megfelelő elővigyázatossággal lehetővé teszi az argon helyett a hidrogént, akkor ez megbízhatóbb védelmet nyújt a rész belső felületének oxidációja ellen.